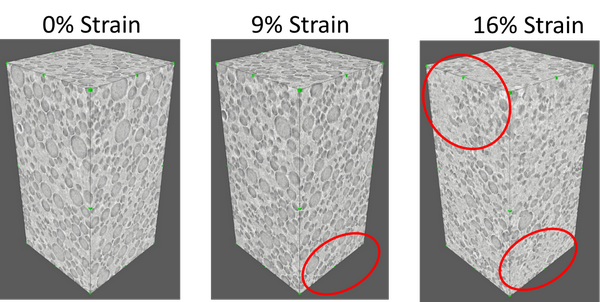
Micro-glass spheres embedded in syntactic foam
Damage evolution in a 0.5 mm × 0.5 mm × 1 mm sample under different strains applied by Deben in-situ testing stage. Regions with severe damage are depicted with red circles.
X-Ray micro computed tomography
CT scanners offer a powerful non-destructive method for three-dimensional imaging of internal structure for a wide range of samples. Examples of application include analysis of porous rocks, materials research across various industries, detection of corrosion, cracks and flaws, assembly inspection of complex mechanisms and visualisation of biological tissues There are two high-resolution X-ray micro computed tomography (CT) machines available at Aberdeen:
|
|
Xradia VersaXRM-410 has a spatial resolution of 0.9 µm, a maximum source of 150 kV, and employs a unique two-stage magnification process that enables true submicron resolution for a wide range of sample sizes. Xradia is equipped with an in-situ tensile/compression/bending testing stage. The combination of the CT and testing stage is employed to quantify mechanical damage progression occurring when a material is strained. |
XT H 225ST Nikon CT scanner is the second CT machine which has a spatial resolution of 3 µm, a maximum source of 225 kV. It is ideal for larger sample dimensions. |
Contact: Dr Mehmet Kartal at |
Contact : Ms Jaime Buckingham at |